Blog
Beware bad processes lurking everywhere!
Let’s play a game
with no prizes 😂
Ever found yourself grumbling about how things are done at work? Maybe it’s that endless approval chain or the complicated way the simplest tasks are handled. If so, we’ve got you!
What Do We Mean by “Bad Processes”?
These are procedures, workflows, or systems that are inefficient, overly complicated, or simply outdated.
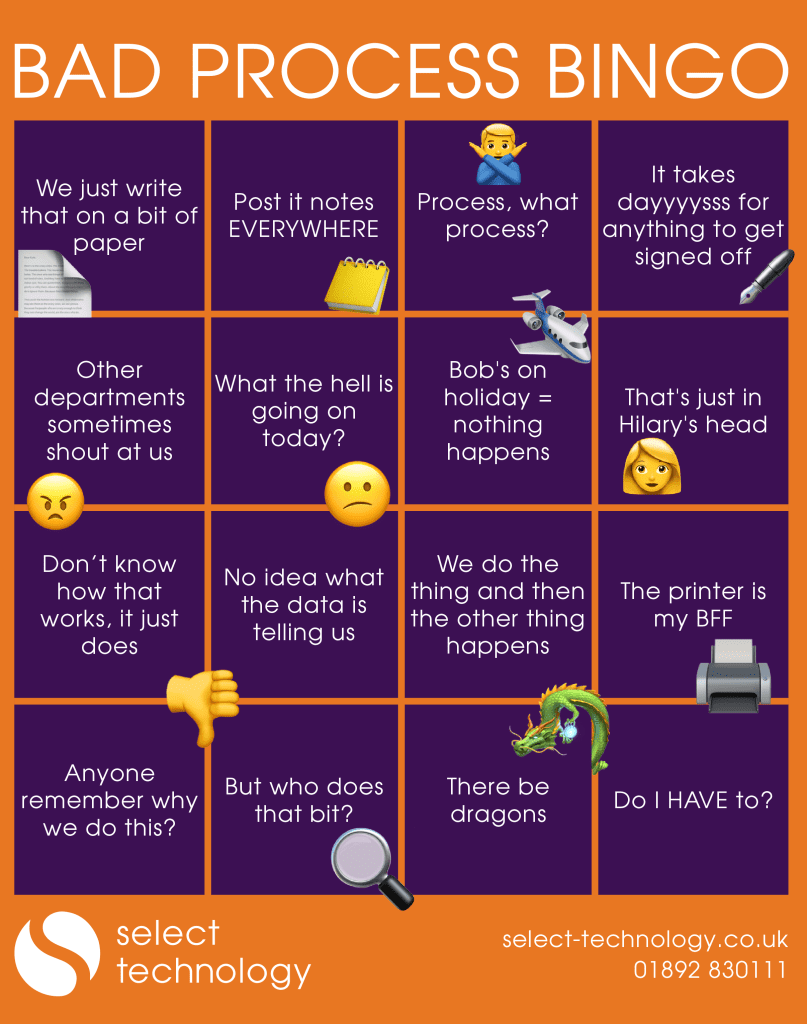
- Red Tape: Layers upon layers of approvals and paperwork that slow everything down.
- Redundant Steps: Tasks that could be streamlined but are bogged down by unnecessary steps.
- Poor Communication Channels: Miscommunication or lack of communication that results in mistakes and delays.
- Lack of Automation: Manual processes that could easily be automated to save time and reduce errors.
How Bad Processes Impact Business Success
You might be thinking, “Okay, so bad processes are annoying, but do they really impact business success?” The answer is a resounding yes. Here’s how:
Kelly’s eye
1. Reduced Efficiency
Inefficient processes are time-wasters. Employees spend more time navigating the complexities of a bad process than actually doing productive work. This inefficiency can lead to missed deadlines, reduced output, and ultimately, higher operational costs.
One little duck
2. Lower Employee Morale
Nothing frustrates employees more than feeling like their time is being wasted. Bad processes can lead to stress, burnout, and a general sense of dissatisfaction.
Cup of tea
3. Increased Errors and Risks
Bad processes are often breeding grounds for mistakes. Whether it’s a manual data entry error or a miscommunication due to poor processes, these mistakes can have costly repercussions in terms of your bottom line as well as risks to safety and compliance.
Knock at the door
4. Customer Dissatisfaction
Inefficiencies don’t just affect the internal workings of a business; they trickle down to the customer experience. Delayed deliveries, poor customer service, and mistakes in orders are just some of the ways bad processes can lead to unhappy customers. And as we all know, a dissatisfied customer is less likely to return.
The Silver Lining: Fixing Bad Processes
The good news is that bad processes can be fixed. Here are some steps you can take:
1. Identify the Problem Areas
The first step to fixing bad processes is identifying where the problems lie. This could be done through employee feedback, customer complaints, or an internal audit.
2. Simplify and Streamline
Once you’ve identified the problematic areas, the next step is to simplify and streamline. This might involve cutting out redundant steps, automating manual tasks, or improving communication channels.
3. Implement Technology
In today’s digital age, there’s a plethora of tools and technologies designed to improve efficiency. Whether it’s project management software, automation tools, or CRM systems, technology can play a big role in fixing bad processes. Yay!!
4. Continuous Improvement
Fixing bad processes is not a one-time thing. It’s an ongoing effort that requires continuous monitoring and improvement. Regularly review your processes and be open to making changes as needed.
If you need some help banishing the bad processes in your business, just let us know! Drop us an email to hello@select-technology.co.uk or give us a call on 01892 830111.